Close to Light Speed
Taking concrete into space sounds strange enough, but how about mixing it on the International Space Station (ISS) in a handmade mixer? Experts at the Institute for Structural Concrete believe the MASON* project will not only help to protect the earth’s environment, but might also enable buildings on the moon. By Jennifer Meina
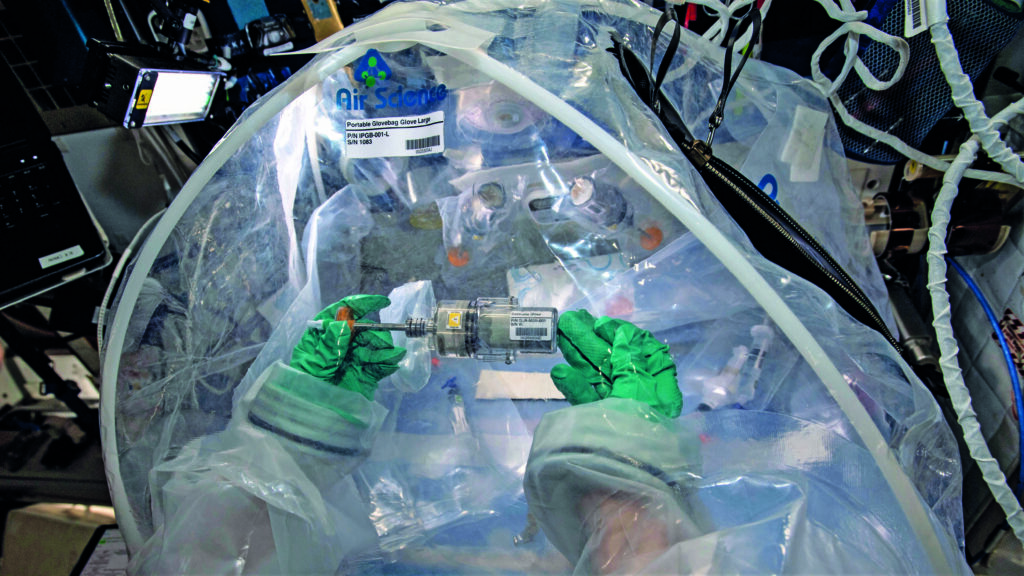
‘Our concrete specimens in the manual mixers we made were very special guests on SpaceX 24 when it flew to the ISS in November 2021,’ says Prof. Dr. Martina Schnellenbach-Held, Head of the Institute for Structural Concrete (IfM). The goal of the UDE team and their partners at the German Aerospace Center (DLR) and the University of Cologne (UzK) is visionary: How can we produce concrete in a more climate-friendly way? Cement in particular, a major component of the material, releases around three gigatonnes of CO2 a year worldwide. It also demands massive amounts of sand, gravel and water. An answer could come from MASON.
But why an experiment in space? Constant weightlessness offers greater insights into the behaviour of materials than are possible in earth-bound laboratories. This is because the strength of concrete depends on both the mixing ratio and the curing process. On earth, solidification and hardening are influenced by gravitation, so the pore structure (amongst other things) and possibly also the strength of concrete depend on gravity. This makes it important to mix the concrete on the ISS, because here – in the laboratory of the space station as it orbits the Earth at an altitude of about 400 kilometres – the conditions of zero gravity always apply. However, neither NASA, the US National Aeronautics and Space Administration, nor any other space agency had a suitable mixer. In the end, the researchers at the UDE had to develop one specially.
Patented tinkering
There were two crucial conditions: 1. It had to be lightweight. Concrete test specimens in the usual dimensions and masses could not have been produced or transported. 2. It had to meet the strict safety requirements. For one thing, the cement must never escape the container, otherwise the ISS would be contaminated with cement particles and the astronauts could be exposed to a health risk. ‘One particularly tricky question was how to mix the dry starting materials, that is, cement and sand, with the water,’ explains Dr. Torsten Welsch of IfM.
But that was far from the only challenge. ‘The safety inspections started with calculations about how the container would withstand various over- or underpressure scenarios and extended to numerous experiments to check that all components were leakproof and unbreakable.’ One test, for example, used a kind of vibrating table to simulate the acceleration the hardware undergoes during the rocket launch. The tests lasted months – and ended successfully; a patent has now been registered for the concrete mixer. ‘We began development in November 2020 and in August 2021 received certification from ESA, the European Space Agency. In space travel terms, that’s close to light speed,’ Welsch emphasises.
The IfM
Prof. Dr. Martina Schnellenbach-Held heads the IfM. With her team of more than 20 employees, she researches the development of new building materials, building systems and reinforcement elements.
Working with simulated moon rock
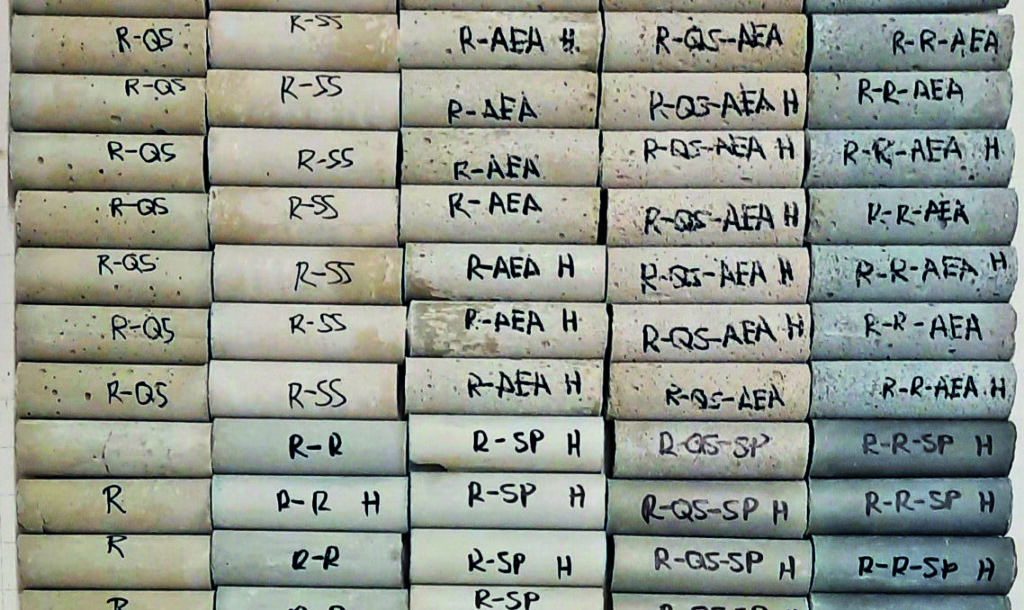
The experiment was also a success: The various concretes were mixed in all the UDE manual mixers by German astronaut Matthias Maurer in February 2022. ‘Matthias Maurer passed word to us that he was very enthusiastic about our experiment and the device. He only complained about a little muscle ache, but you can’t blame him after mixing 64 samples by hand,’ jokes Schnellenbach-Held. All the mixtures came from IfM. ‘It was important to us to see how conventional concrete behaves under zero gravity. With a view to the construction of stations on the Moon, however, we also used regolith, a simulated moon rock, for example.’
The UDE researchers are now anticipating the return of the hardened MASON project samples to Germany, where they will be subjected to extensive analysis in the laboratories of the IfM and the University of Cologne. One especially interesting aspect is that the same trials took place on earth in parallel with the experiments on the ISS – both conventionally under gravity and in clinostats, which simulate zero gravity. If the results from space and the clinostats are comparable, then in future it may be possible to conduct numerous experiments faster, more easily and more affordably – they wouldn’t have to be flown into space.
There are no concrete plans for a follow-up project yet, ‘but since building habitation on the moon is a declared goal of NASA’s Artemis Mission, there’s definitely still a lot of work to be done. One important subject for instance is reducing or eliminating the need for water – a very scarce resource in space,’ continues Schnellenbach-Held, who finds it ‘extraordinarily exciting’ tackling construction on celestial bodies scientifically. ‘We’re proud to be able to make a contribution.’
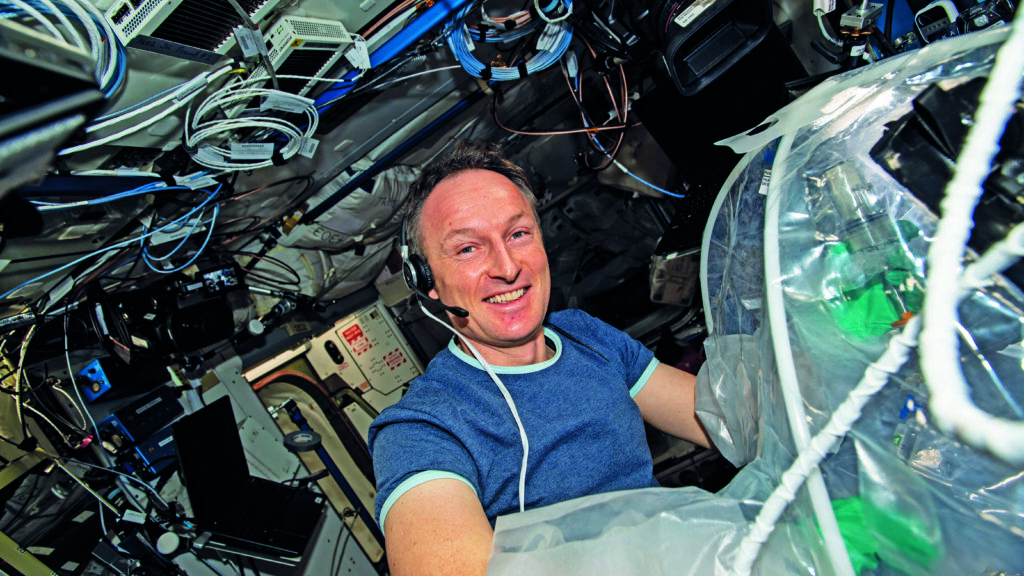
Concrete of the future
Isn’t concrete obsolescent though? Shouldn’t we be looking for alternatives? That’s difficult, she says. ‘Despite all the discussions, I don’t believe that concrete will be replaced as a construction material in the foreseeable future. There’s no other material with comparable properties – from stability to enormous longevity.’ Alternative construction methods using wood or steel, for instance, cannot completely replace concrete construction simply because of a shortage of resources. ‘But we are optimistic that we will succeed in improving the sustainability of concrete.’ And in concrete research that’s one of the essential questions – including at the UDE, where the IfM’s research ranges from ‘classic’ construction questions about the use of artificial intelligence in concrete structure engineering through to the development of high performance concrete.
»Despite all the discussions, I don’t believe that concrete will be replaced in the foreseeable future.«
The latter includes concepts such as high performance aerogel concrete, a more sustainable and at the same time more heat insulating lightweight structural concrete, which makes it unnecessary to use composite thermal insulation systems.
* MASON stands for ‘Material science on solidification of concrete’ – material research on concrete in zero gravity