Im Herzstück der Hochfrequenztechnik
Hautkrebs erkennen, den Wassergehalt einer Pflanze bestimmen, Materialdicke messen oder riesige Datenpakete verschicken. Die Einsatzmöglichkeiten von Terahertz (THz)-Wellen sind riesig – ähnlich wie die Kosten für Herstellung und die Ausrüstung. Noch, denn in Duisburg tut sich etwas. Ein Rundgang.
Von Jennifer Meina
Alles aus einer Hand. Daran arbeitet Dr. Nils Weimann mit seinem Team. Der Professor für Halbleitertechnologie an der Fakultät für Ingenieurwissenschaften und Leiter der Arbeitsgruppe Bauelemente der Höchstfrequenztechnik baut mit drei Kollegen an der UDE ein deutschlandweit einmaliges Terahertz-Integrationszentrum auf. „Wir bilden mit weiteren Netzwerkpartnern vor allem aus NRW einen international anerkannten Knotenpunkt der Terahertz-Forschung.“ Ein Standortvorteil ist, dass die gesamte Technologiekette hier angesiedelt ist: von der Herstellung des Halbleitermaterials über die Fertigung der Chips bis hin zur Anfertigung der Module und der speziellen THz-Messtechnik. Dafür fließen über sieben Millionen Euro Landes- und EU-Mittel in das Zentrum für Halbleitertechnik und Optoelektronik (ZHO) nach Duisburg. „Terahertz-Wellen werden dazu beitragen, mehr Kapazität in zukünftigen mobilen Kommunikationsnetzwerken bereitzustellen – Stichwort 6G. Aber die Technik kann viel mehr als nur Hunderte von Gigabit pro Sekunde übertragen“, betont Weimann. „Sie ermöglicht es etwa, dass Roboter und Maschinen die Position von Objekten präzise bestimmen und gleichzeitig etwas über deren Materialeigenschaften erfahren können. Die schnellen Wellen haben riesiges Potenzial.“
1. MATERIALANALYSE: WIE AUS GAS EIN SCHALTKREIS WIRD
Terahertzstrahlen sind elektromagnetische Wellen, die zwischen Infrarotstrahlung und Mikrowellen liegen. Doch anders als für ihre Wellen-„Nachbarin“ mit kleineren oder größeren Frequenzen existiert bislang noch keine Chiptechnologie, die diese Strahlung effizient und damit kostengünstig verarbeiten kann. Das wollen die Duisburger ändern.
Die Halbleiterproduktion beginnt in den Reinräumen des ZHO – genauer: in der Epitaxieanlage, die von Doktorand Alexander Poßberg bedient wird (Bild 1). Hier wird ein Wafer aus Indiumphosphid eingelegt. „Üblicherweise bestehen Wafer in der Chiptechnologie aus Silizium, aber unser Halbleitermaterial eignet sich besser für höchste Frequenzen“, erklärt Weimann. Diese Wafer sind das Gerüst, die Grundplatte der Chips, die hundertfach auf einem Wafer entstehen. Auf der hauchdünnen, runden Scheibe, die etwa handtellergroß ist, werden im sogenannten Epitaxieverfahren spezielle Kristallschichten aufgetragen. Über den Wafer wird dabei ein Gas geleitet, das zunächst individuell gemischt wird (Bild 2). Unter Wärmeeinwirkung zersetzt es sich in einzelne Atome, die sich – Lage für Lage – auf den Wafer legen. Über die Konzentration der Moleküle im Gasstrom kann die Kristallzusammensetzung eingestellt werden. Das alles wird am Computer gesteuert. Der Wafer besteht nun aus mehr als 30 Schichten verschiedener Materialien, von denen einige nur wenige Nanometer dick sind (Bild 3).
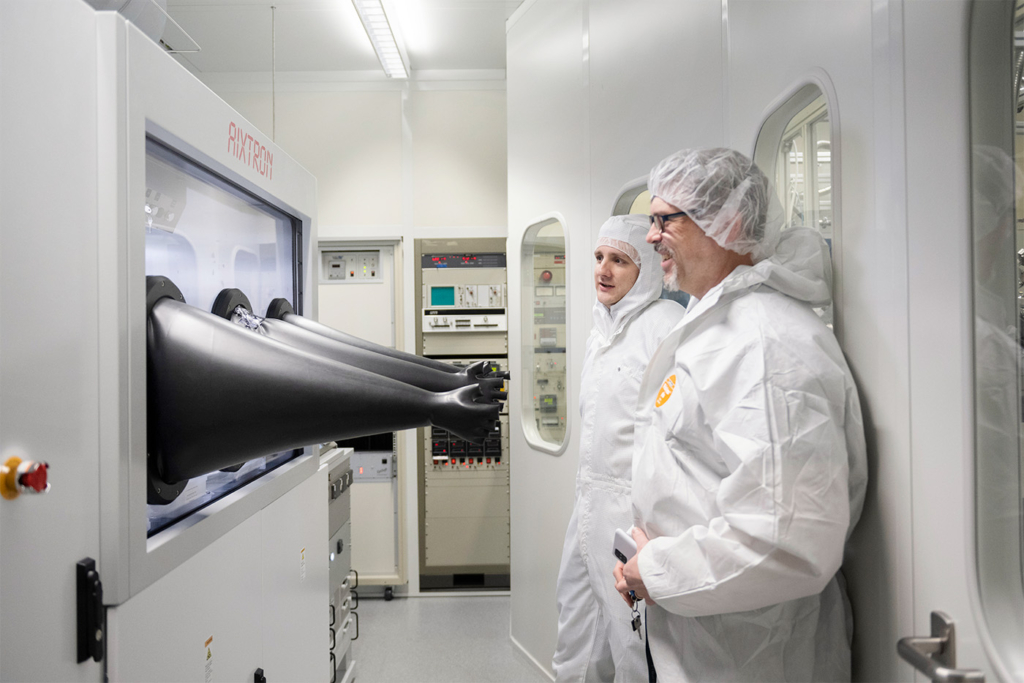
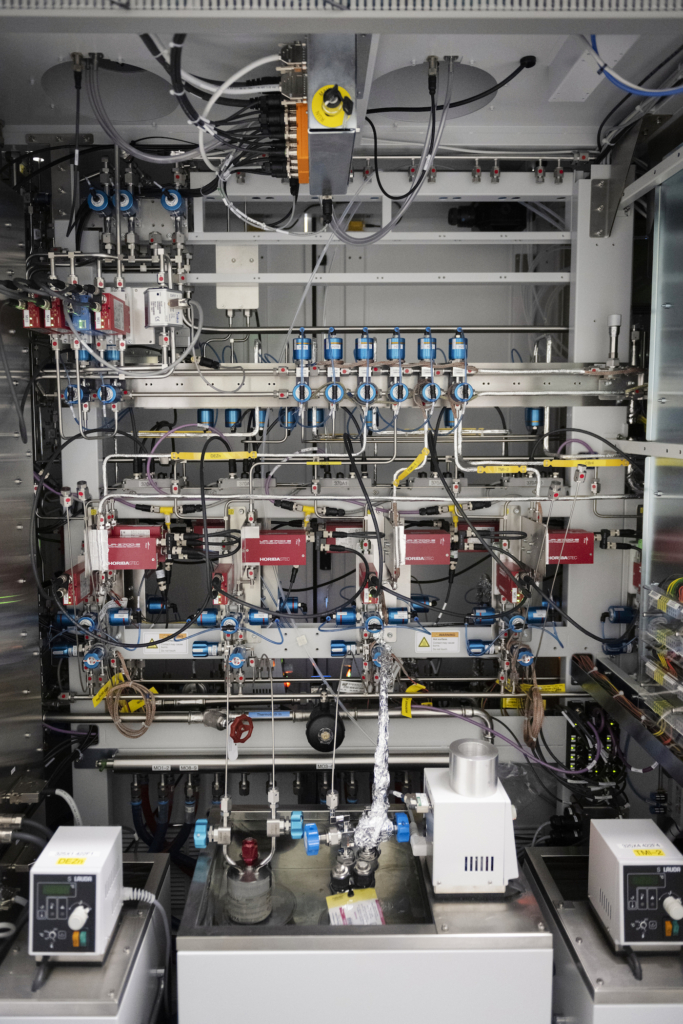
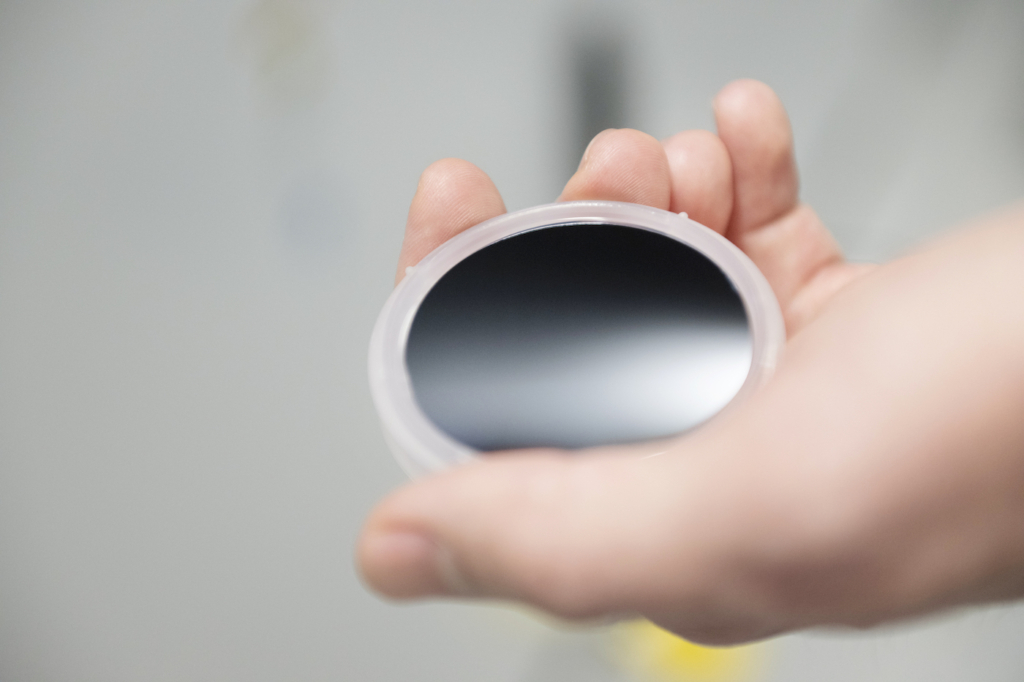
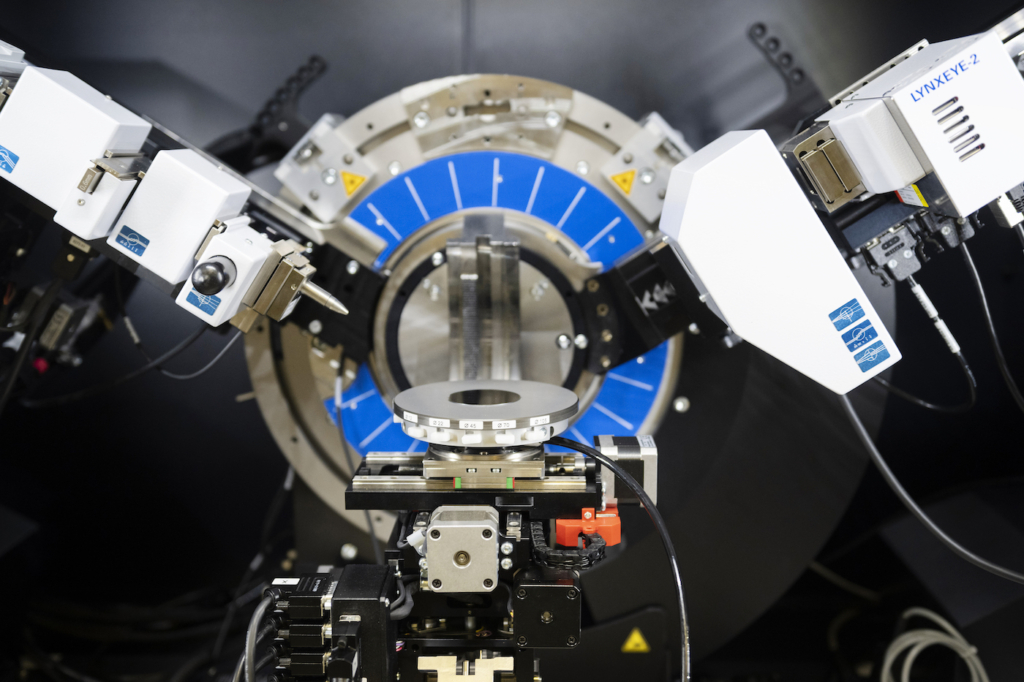
Wie gut eignet sich die Zusammensetzung als Ausgangsmaterial für Halbleiterbauelemente? Das wird im Röntgendiffraktometer analysiert (Bild 4). Mit diesem Verfahren werden die Abstände der Atome zueinander und die Dicke der Einzelschichten auf einen Atomabstand genau gemessen.
Sind die Analyse-Ergebnisse vielversprechend, folgt die Fotolithografie, mit der mikroskopisch kleine Strukturen auf der Wafer-Oberfläche geschaffen werden. Dazu wird eine lichtempfindliche Schicht auf die Wafer aufgebracht und anschließend durch verschiedene Fotomasken (Bild 5) belichtet. Die Masken bestehen aus Glas mit einer Chromschicht, in die Öffnungen eingearbeitet sind. Mit dieser Methode kann eine Struktur auf beliebig vielen Wafern wiederholt werden, ähnlich der Lithografie, die aus dem Buchdruck bekannt ist. In 10 bis 20 Produktionsschritten entsteht die notwendige Struktur auf dem Wafer, um einzelne Bauelemente durch Ätzverfahren zu isolieren und mit Metallkontakten zu versehen. Mit UV-Belichtung lassen sich so Strukturen um einen Mikrometer – ein Hundertstel des Durchmessers eines Haars – herstellen. „Es geht aber noch hundertmal kleiner: mit unserer neuen Elektronenstrahllithografie können wir Strukturen mit unter zehn Nanometer Größe definieren. Das sind ungefähr 25 Atomabstände im Kristall oder ein Zehntausendstel eines Haardurchmessers“, sagt Weimann.
Direkt gegenüber dem Röntgengerät (Bild 6), das sich die Forscher gerade anschauen, befindet sich die speziell angefertigte Metall-Beschichtungsanlage (l.), in die die Waferstücke eingelegt werden. Der Luftsauerstoff stört den Prozess – deswegen können die Wissenschaftler:innen wie Doktorand Enes Mutlu in die Anlage auch nur über integrierte Handschuhe eingreifen (Bild 7). In einer Stickstoffatmosphäre werden die Wafer mit Metall bedampft – so entstehen stromleitende Kontakte auf dem Chip.
Diese Waferstücke enthalten Hunderte von Terahertz-Sendern und -Empfängern mit integrierten Antennen (Bild 8). Ein einzelner Sender ist nur im Mikroskop zu sehen (Bild 9).
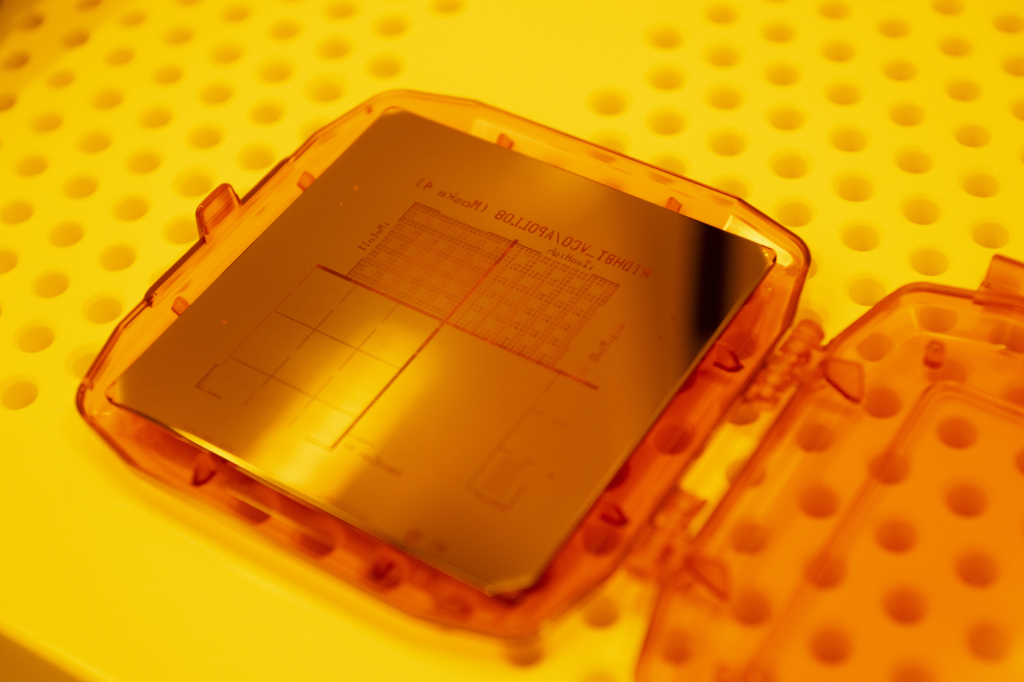
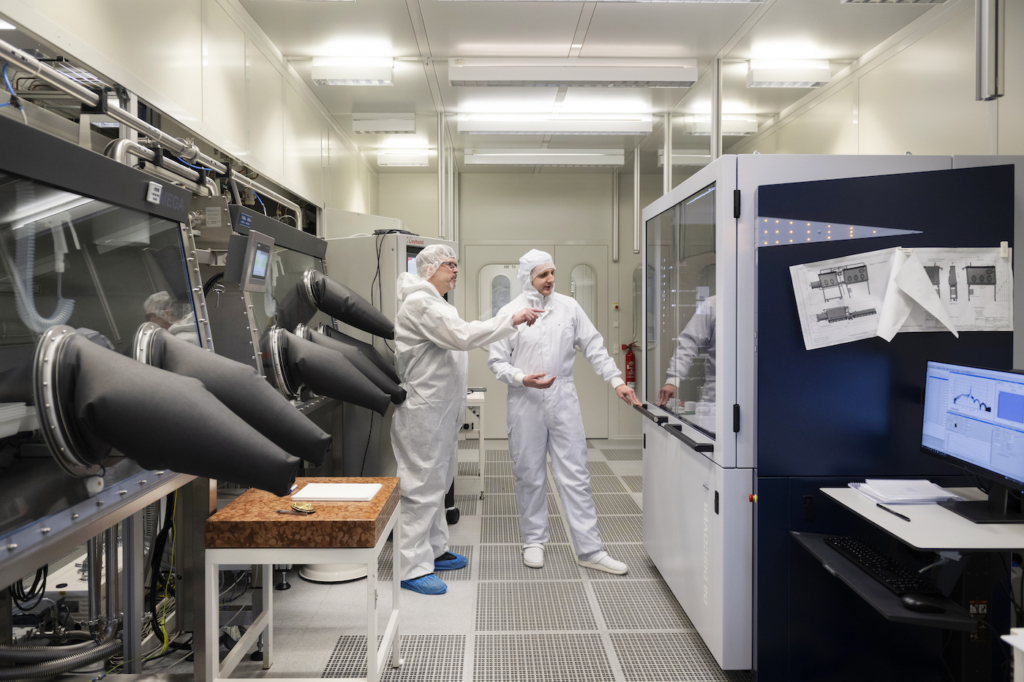
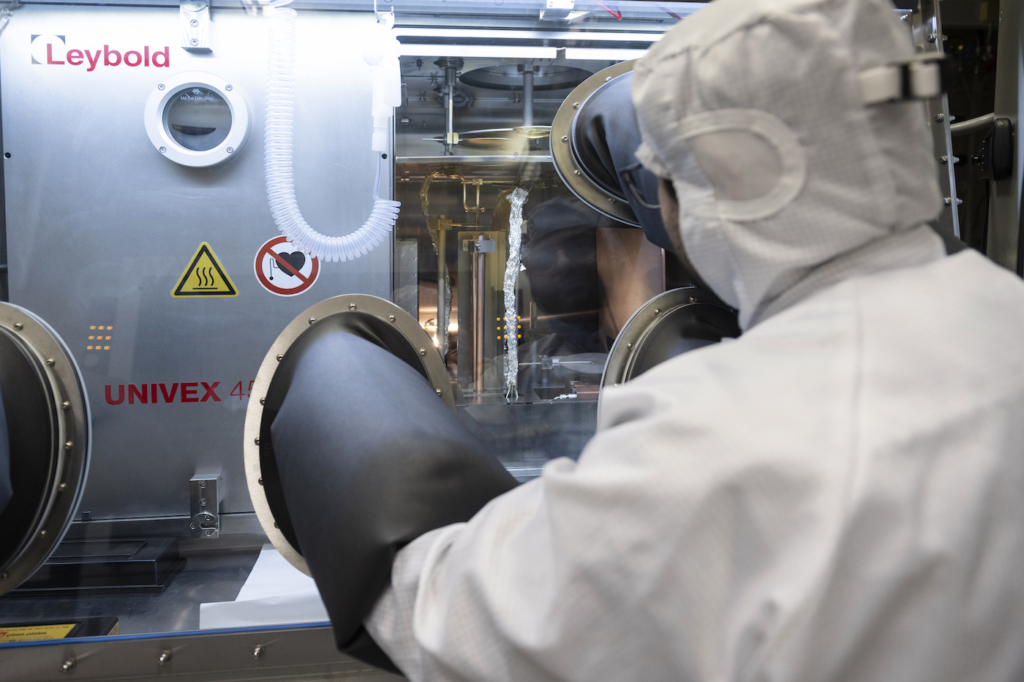
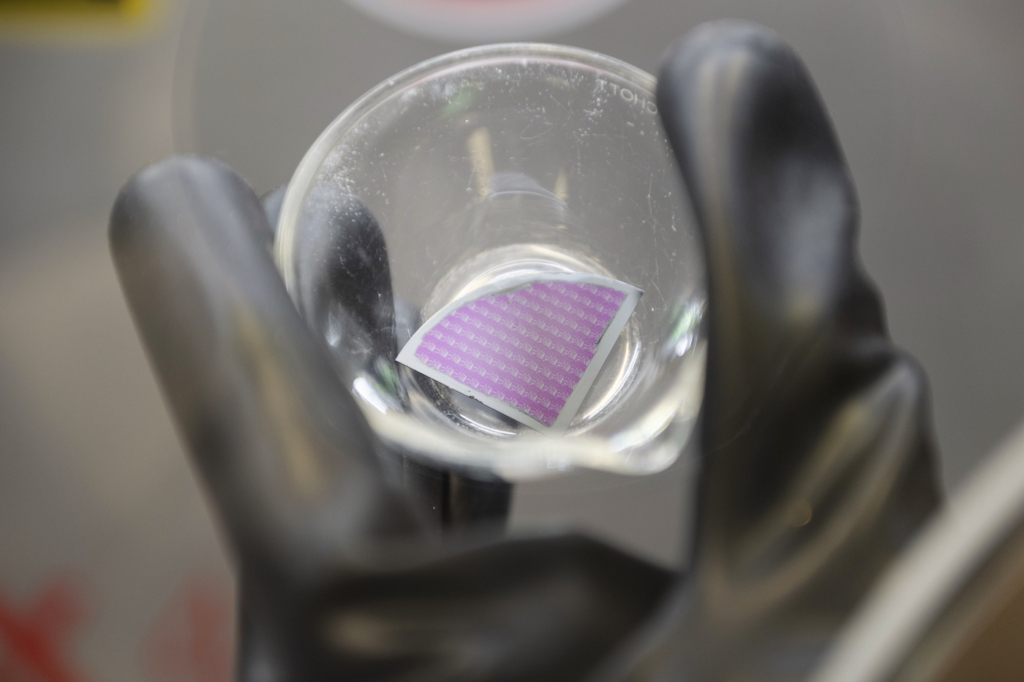
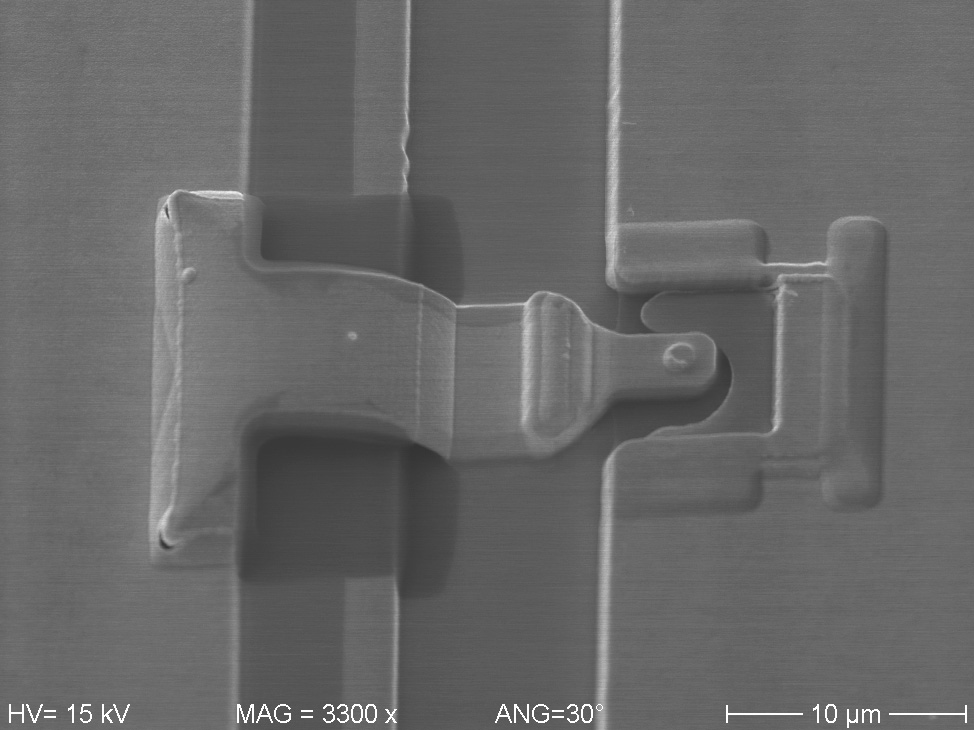
2. MESSUNG – DIE SPANNUNG STEIGT
Beim elektrischen Funktionstest wird untersucht, ob der Herstellungsprozess erfolgreich war. Unter 10.000-facher Vergrößerung werden feinste Nadeln auf die Chipoberfläche gesetzt, und mit speziellen Messgeräten wird die Aussendung von THz-Wellen überprüft (Bild 10).
Zur Integration in größere Messaufbauten werden die winzigen Chips auf Platinen montiert, um Anwendungen wie z.B. die Kontrolle von Lackdicken in der Autoherstellung zu realisieren oder die Überwachung des Wasserhaushalts von Pflanzen zu erforschen. Mit bloßem Auge muss man schon genau hinsehen: Die winzigen, goldenen Quadrate auf der Mittellinie der Platine – das sind die Chips (Bild 11).
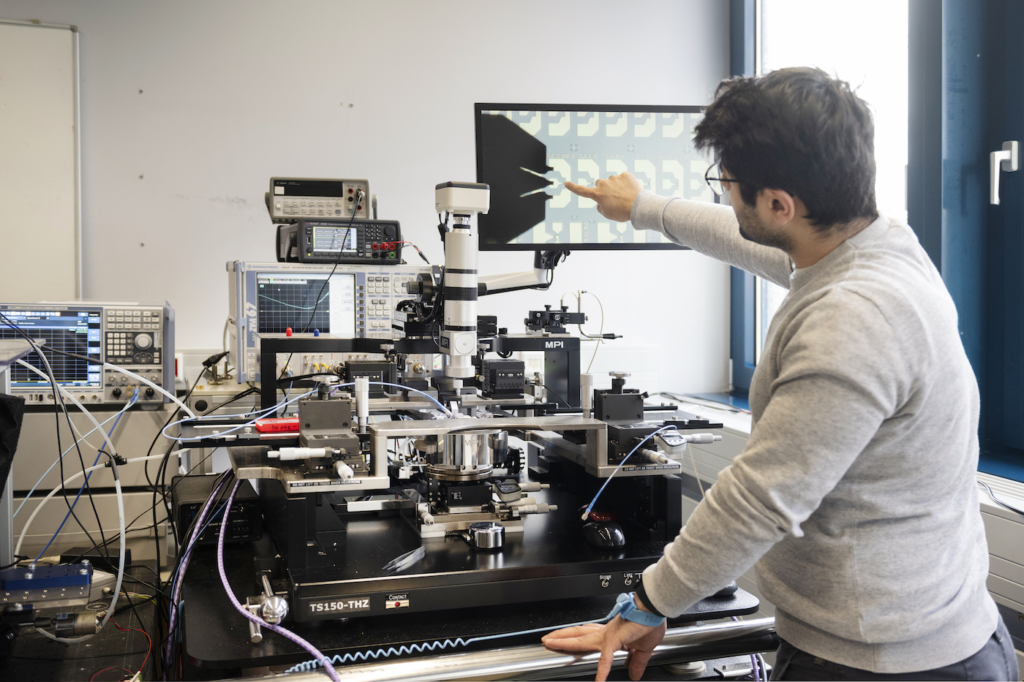
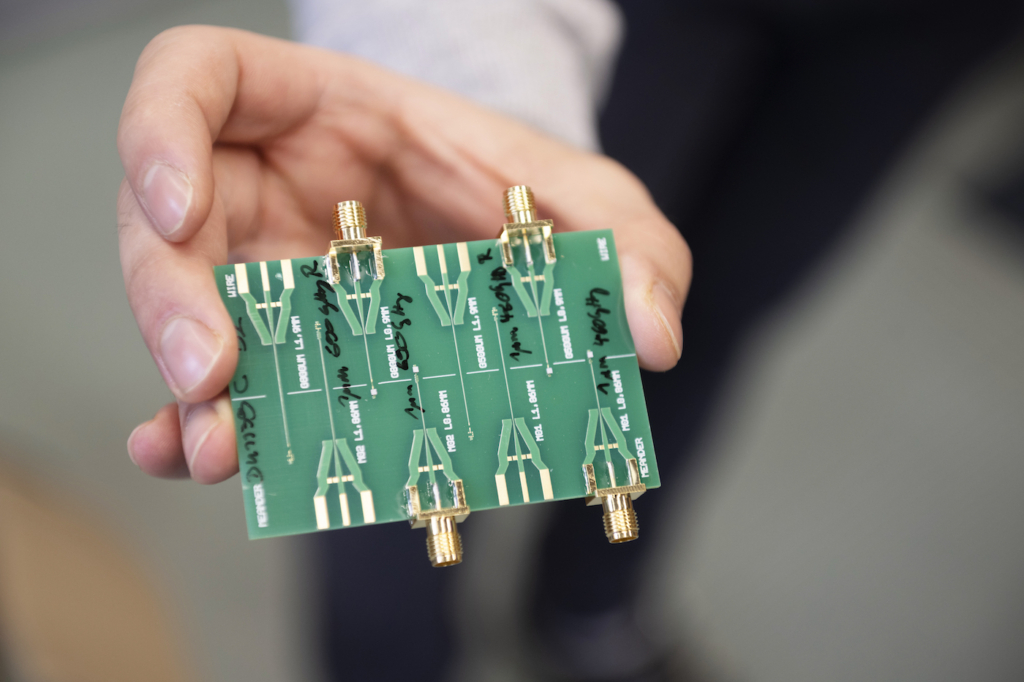
3. MODULHERRSTELLUNG: NICHT VON DER STANGE
Die Platinen (Bild 11) eignen sich gut zur Nahfelderkundung, z.B. auch zur Integration in Instrumente, mit denen sich die Hautoberfläche darstellen lässt. Terahertz ist für medizinische und biologische Anwendungen gut geeignet, da die Strahlung keine Schädigung des Gewebes hervorruft.
Um weitere Strecken zurückzulegen, werden spezielle Terahertz-Module mit integrierten Richtantennen benötigt (Bild 12). Derzeit kostet ein Terahertz-System so viel wie ein Luxusauto – etwa 50.000 bis 100.000 Euro – und hat die Ausmaße eines Kühlschranks. Künftig werden die Sender und Empfänger nicht nur wesentlich günstiger – nur noch einige hundert Euro-, sondern auch sehr viel energieeffizienter und um mehrere Dimensionen kleiner. In den UDE-Modulen werden die Terahertz-Wellen in Luftkanälen mit einem halben Millimeter Breite und Höhe geleitet. Die Kanäle sind auf allen Seiten mit Metall umschlossen, wie ein rechteckiges Rohr. In einem THz-Modul werden die Signale von mehreren Chips über solche Kanäle kombiniert – das bringt mehr Sendeleistung und ermöglicht auch die Richtungssteuerung der Terahertz-Strahlen, die aus dem Modul austreten. Die Kanäle werden mit hoher Präzision, auf einen Mikrometer genau, in das Metall gefräst. Dazu braucht es eine spezielle Fräse, die nicht nur State-of-the-art ist, sondern die es so auch nur an der UDE gibt (Bild 13).
Hier kann Doktorand Konrad Müller nun mittels 3D-Plan das gewünschte Modell des Moduls erstellen und in der Fräse umsetzen (Bild 14). „Mit der Mikropräzisionsfräse können wir schmale Gräben in einer Breite von 100 bis 300 Mikrometern in Metallblöcke einbringen, also so breit wie ein bis drei Haare“, erklärt Weimann.
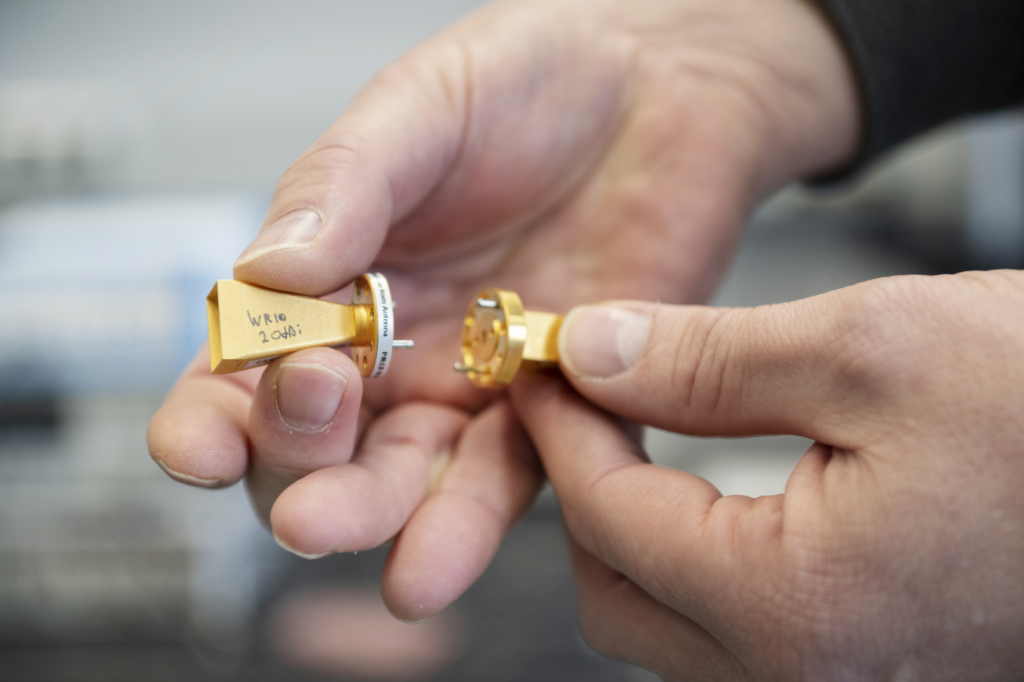
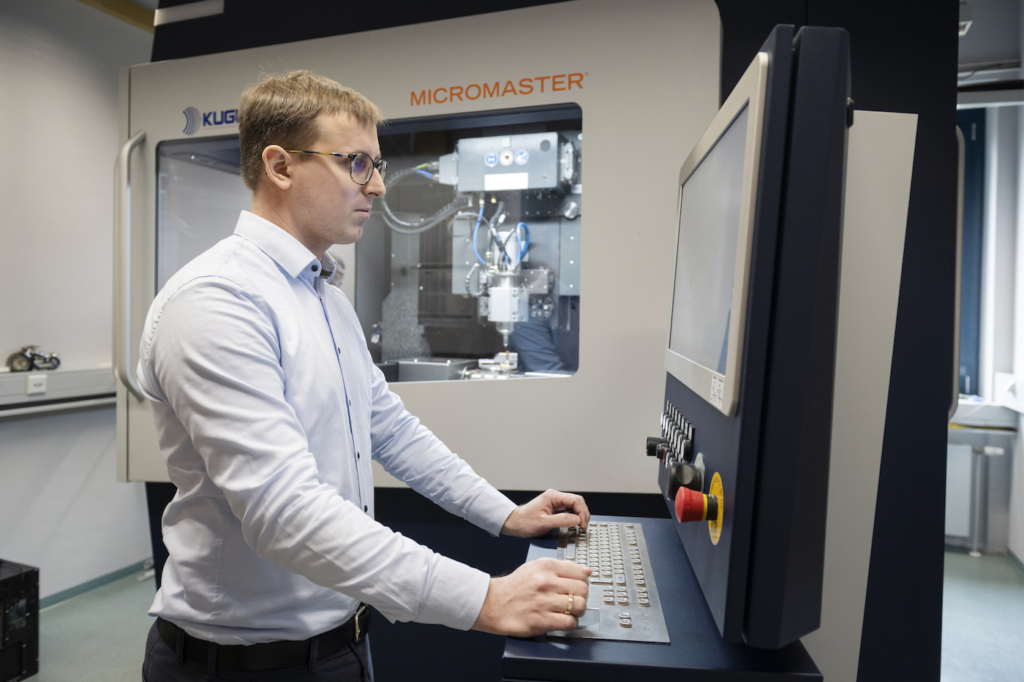
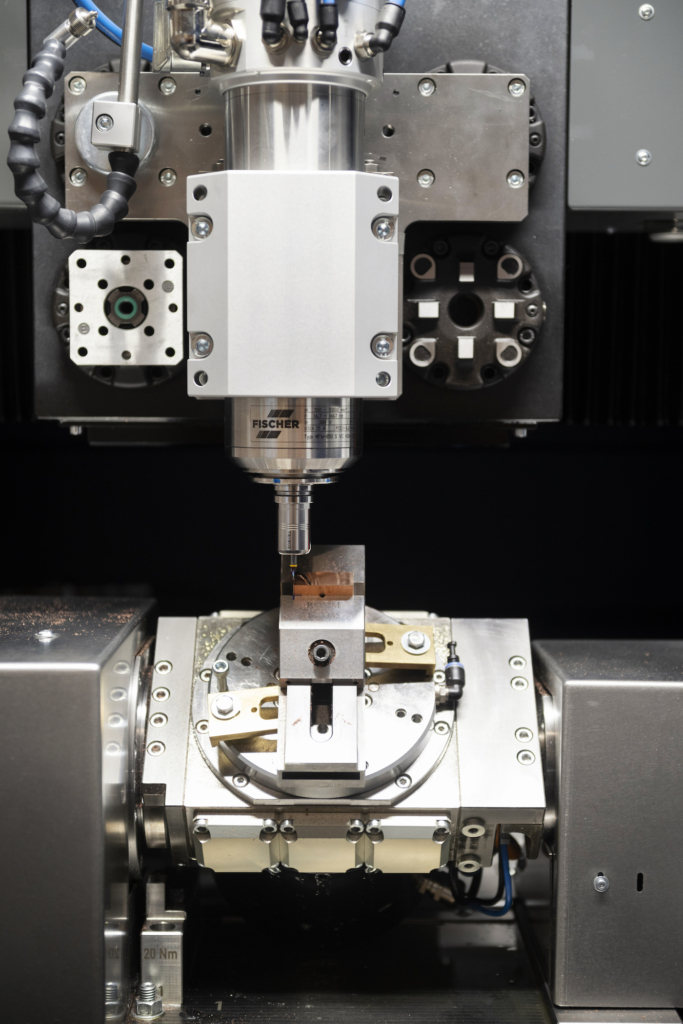
Nach dem genauen Fräsen der Gräben werden diese mit einem Metalldeckel verschlossen – so entstehen die schmalen Kanäle, auch als Hohlleiter bezeichnet, in denen die Terahertz-Wellen zwischen den Halbleiterchips und zur Antenne geführt werden.
Noch ist das UDE-Team in der Forschungsphase, der Weg zur Marktreife dauert noch. Weimann rechnet damit, dass die hier entstehende effiziente Terahertz-Chiptechnologie in etwa fünf bis zehn Jahren in der Industrie eingesetzt werden kann. „Terahertz ist ein großer Teil des gesamten elektromagnetischen Spektrums, der jedoch aufgrund fehlender Komponenten kaum genutzt wird. Die Terahertz-Wellen schädigen kein Gewebe, können große Datenmengen übertragen und Materialoberflächen unterscheiden. Die kurze Wellenlänge ermöglicht zudem kleine Antennen. In der Kombination dieser Eigenschaften ergeben sich viele neue Anwendungen, auch solche, die wir heute noch nicht auf dem Schirm haben.“ Dies ist hier ein großes Thema: der DFG-Sonderforschungsbereich MARIE, das BMBF-Netzwerk 6G-HUB 6GEM sowie das NRW-Forschungsnetzwerk terahertz.nrw befassen sich in Duisburg mit neuen Terahertz-Anwendungen, die auf die entstehenden Technologien aufbauen.
Um die besonderen Anforderungen der UDE-Forschenden zu erfüllen, wurde die Fräse extra angefertigt. Und im Oktober 2022 wurde sie in luftiger Höhe im ZHO angeliefert: Da die etwa 3m³ große und vier Tonnen schwere Fräse nicht in den Aufzug passt, hievte sie ein Kran direkt in den Raum – durch ein Loch in der Gebäudewand.
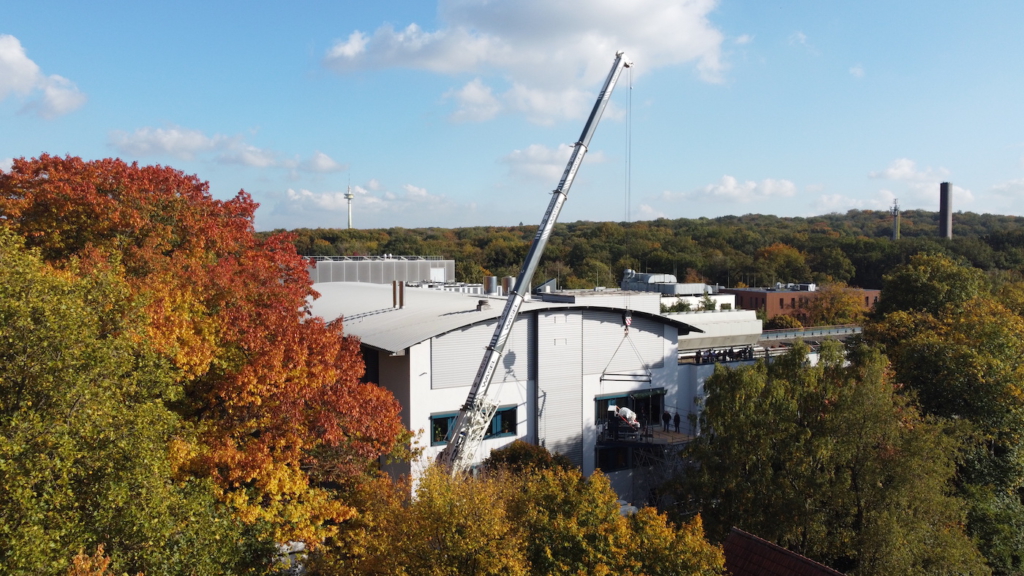
Titelbild: © Bettina Engel-Albustin